Mediaroom
Breve descrizione della sezione
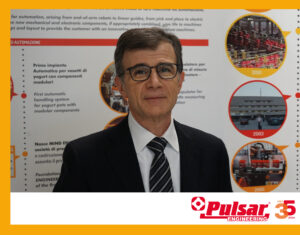
Intervista a Massimo Franzaroli, fondatore di Pulsar Engineering: 35 anni di Innovazione e Sfide
Intervista a Massimo Franzaroli, fondatore di Pulsar Engineering: 35 anni di Innovazione e Sfide Massimo Franzaroli, mente visionaria ed esperto nel settore dell’ingegneria, celebra quest’anno
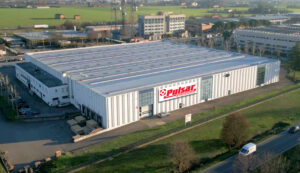
Una nuova sede all’insegna dell’efficienza
Da sempre, Pulsar Engineering pone al centro dei suoi valori il costante miglioramento e l’ottimizzazione dei processi. Questo impegno non si limita a fornire soluzioni all’avanguardia nel
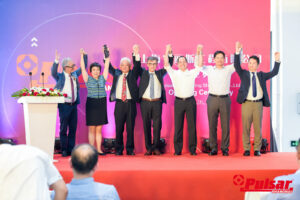
I pionieri del tissue si incontrano all’inaugurazione di Pulsar Shanghai
A destra, il sig. Shinoara, vicepresidente dell’azienda Kawanoe Zoki, che produce macchine per la carta tissue in Giappone dal 1944; il sig. Michael Zhao, amministratore
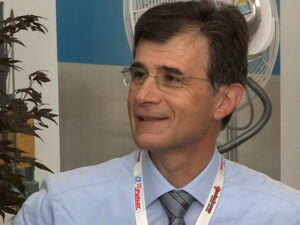
30 anni di automazione, grazie a tutti voi!
Massimo Franzaroli celebra i suoi primi 30 anni nel mondo dell’automazione ripercorrendo le tappe che hanno portato al successo di quella che oggi è Pulsar.
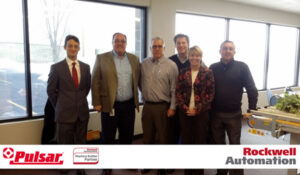
Pulsar e Rockwell Automation rafforzano la loro partnership
(Da sinistra: Mr. Massimo Capisani – Vice Presidente di Pulsar America, Mr. Thomas A. Tengowski – Account Manager per Rockwell Automation, Mr. Tim Clague –
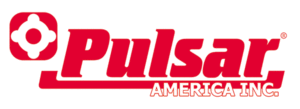
Pulsar America sposta la propria sede a Green Bay
A distanza di due anni dall’apertura dell’ufficio di Appleton, Pulsar America Inc. annuncia una nuova evoluzione delle proprie attività negli USA. Per poter migliorare la