Mediaroom
Breve descrizione della sezione
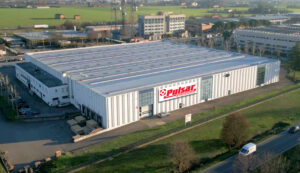
A new headquarter, based on efficiency
Pulsar Engineering has always placed constant process improvement and optimization at the core of its values. This commitment is not limited to providing cutting-edge solutions in
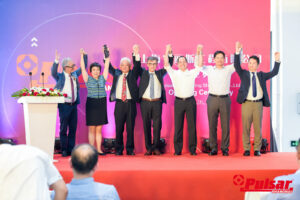
Tissue pioneers met at the inauguration of Pulsar Shanghai
From the right side, Mr. Shinoara, Vice President of the company Kawanoe Zoki, that manufactures Tissue Paper machinery in Japan since 1944; Mr. Michael Zhao, CEO of Toscotec
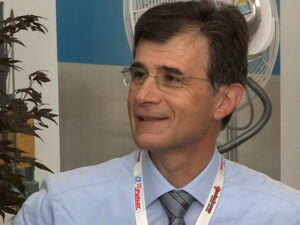
30 years of automation, thanks to all of you!
Massimo Franzaroli celebrates his first 30 years in the automation industry by retracing the steps that led to the success of Pulsar. Thanks to those,
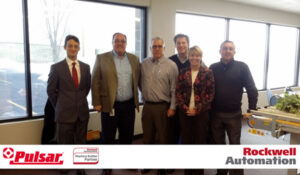
Pulsar and Rockwell Automation USA strengthen their partnership
(From the left: Mr. Massimo Capisani – Vice President of Pulsar America, Mr. Thomas A. Tengowski – Account Manager at Rockwell Automation, Mr. Tim Clague
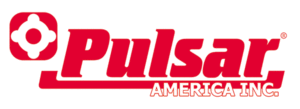
Pulsar America announces its move to Green Bay
After two years of activity in Appleton, in order to grant a better support to the North American market, Pulsar America Inc. is pleased to inform
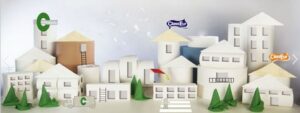
Success Story – Centralcarta
Centralcarta has gained market shares in the Italian and International tissue paper manufacturers’ market with its products dedicated to the professional and consumer world of paper